
Collaborative Robot Risk Assessments
Collaborative robots, also known as cobots, are rapidly transforming the manufacturing industry. These robots are designed to work alongside human workers, providing support and assistance to improve efficiency and productivity. However, with the increasing use of cobots in manufacturing, safety concerns have become a critical issue.
Cobots are different from traditional industrial robots, as they interact with humans in close proximity. Therefore, it is essential to ensure that cobots are safe for human workers
Deploying cobots or upgrading automation?
We'll help you assess risks, validate safety, and comply with ISO/TS 15066 and BS EN ISO 10218-2
Let's make collaboration safe
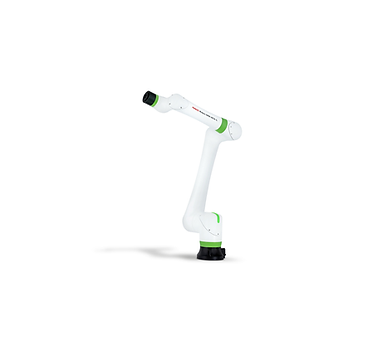
Is Your
Cobot Safe?
Understanding the Risks of Cobots
Collaborative robots can be a great asset to a business, however it is important to understand the risks associated with them. Although there is lots of information available regarding the safety of collaborative robots, it is often overlooked due to the way they have been marketed.
Designed to work alongside humans, collaborative robots are generally considered to be safe. It is important to consider how end tooling and grippers may change the safety risk posed by the cobot. A detailed risk assessment should be completed to ensure the safety of the operators working around them. Consideration should be given to the risks that may occur during the collaborative robots cycle, its end of arm tooling, its movements and the human interaction.
If the cobot is being used truly collaboratively, with no other safety components (light curtains, laser scanners), force and pressure testing must be conducted. The amount of force and pressure that can be exerted in a collision could result in injury. Different parts of the body can receive different forces and pressures, detailed in ISO TS 15066, and it is the scope of the risk assessment to define these points.
As collaborative robots are lightweight and portable they can have a variety of uses within the same work environment. For each separate task and location, a risk assessment should be completed.

STEPS TO COMPLIANCE
01
Assessing your collaborative robot application
As a leading safety consultancy, we understand the importance of conducting a thorough risk assessment. Our team of experienced professionals will inspect your collaborative robot application and identify any risks or hazards. We will also assess as to whether force and pressure testing is required.
02
Report Creation
Our Collaborative Robot Risk Assessment report follows the BS EN ISO 10218-2 and ISO TS 15066 standards and is designed to identify and eliminate potential hazards on your application. With our extensive experience and expertise, you can trust us to produce a report that is both accurate and thorough.
03
Ongoing Support
Long-term partnerships are at the heart of our safety consultancy's ongoing support. Our team of experts provides practical advice and customised solutions to help you establish and maintain a safe workplace. With our focus on building long-term relationships, you can be confident that we'll be there for you every step of the way.
Collaborative Robot Force And Pressure Testing
Force and pressure testing may seem like an extra step, but it's a proactive investment in safety that can prevent accidents, protect your workforce, and ultimately, ensure a smooth and productive operation with your collaborative robot.
When a collaborative robot is using the power and force limiting function (PFL) as a risk reduction method, force and pressure testing is required to validate the contact scenarios.
The amount of force and pressure that can be exerted in a collision could result in injury. Different parts of the body can receive different forces and pressures, as detailed on ISO TS 15066.
Our cobot force and pressure testing service enables us to accurately measure the quasi-static and transient contacts identified and highlighted during the cobot risk assessment and ensure that the values are below limit thresholds specified in ISO TS 15066.
During the commissioning stage, if a collaborative robot is using the power and force limiting function (PFL) as a risk reduction method, it is important to validate the forces and pressures that can be exerted by the cobot movements. Annex A of ISO TS 15066 lists the permissible transient and quasi-static contacts (force and pressure values) that can be exerted onto the body. Where the values are above the permissible limits, measures must be put in place to reduce the values to the acceptable level. This is to ensure that in the unlikely event of a collision with the cobot, the operator is unharmed.
Our experienced safety consultant uses specialist calibrated testing equipment to ensure accuracy and reliability of your system. We are committed to providing you with the highest quality of testing services to ensure the safety of your cobot application.
![]() | ![]() | ![]() | ![]() | ![]() | ![]() |
---|---|---|---|---|---|
![]() | ![]() | ![]() | ![]() | ![]() | ![]() |
What Our Customer's Say
“Cobots and Machinery Safety have been adopted within our business as the go to source for information around safety compliance within the relatively new field of collaborative robots. It’s been an absolute pleasure working with Matt to ensure that we, as a company, remain up to date with the best practice techniques for cobot use within real world applications; and more importantly the latest safety legislation relating to the new technology.
In detail, we have worked with Cobots and Machinery Safety to ensure our technical and sales employees are fully educated and can speak to clients confidently and with accuracy. So far, the engagement has led to further development within our own product range and the systems we employ to provide safe reliable systems to the market. We have on countless occasions recommended Cobots and Machinery Safety to our customer base, and will continue to do so.”
Oliver Selby
Robotics Business Development Manager - Fanuc